The Mystery of Indoor Water: Leak or Condensation?
A leak is when water seeps through cracks, pinholes, or seams in a roof. Condensation is when water accrues on the interior of the building due to outdoor temperatures swings. Condensation is the result of poor insulation, ventilation issues, or high indoor humidity while a leak is the result of a failure point in the roof. Roof condensation often gets mistaken for a roof leak because they both cause water to drip inside a building, but they have different causes and slightly different solutions.
Condensation occurs when a poorly insulated roof is exposed to extreme cold before a fast warm-up. The quick increase in temperature causes condensation to appear when warm, humid air inside the building contacts the cold roof’s surface. If that section is not well dried out via ventilation, the condensation sits which both weakens the building’s structure and causes mold to grow.
Condensation is likely to occur during the spring since it needs temperature swings to appear. But its formation is not always related to a rainstorm or melting snow. However, a leak shows itself during any season after a rainstorm or when snow is melting in the spring. Another difference between condensation and leaks is that leaks are more localized than condensation – they will drip from the same location each time – and are also heavily influenced by the quantity of rain falling or amount of snow melting.
As an experienced roofing contractor for condensation problems, SR Commercial Roofing can help diagnose and resolve these issues whether the issue is a leak or a condensation problem.
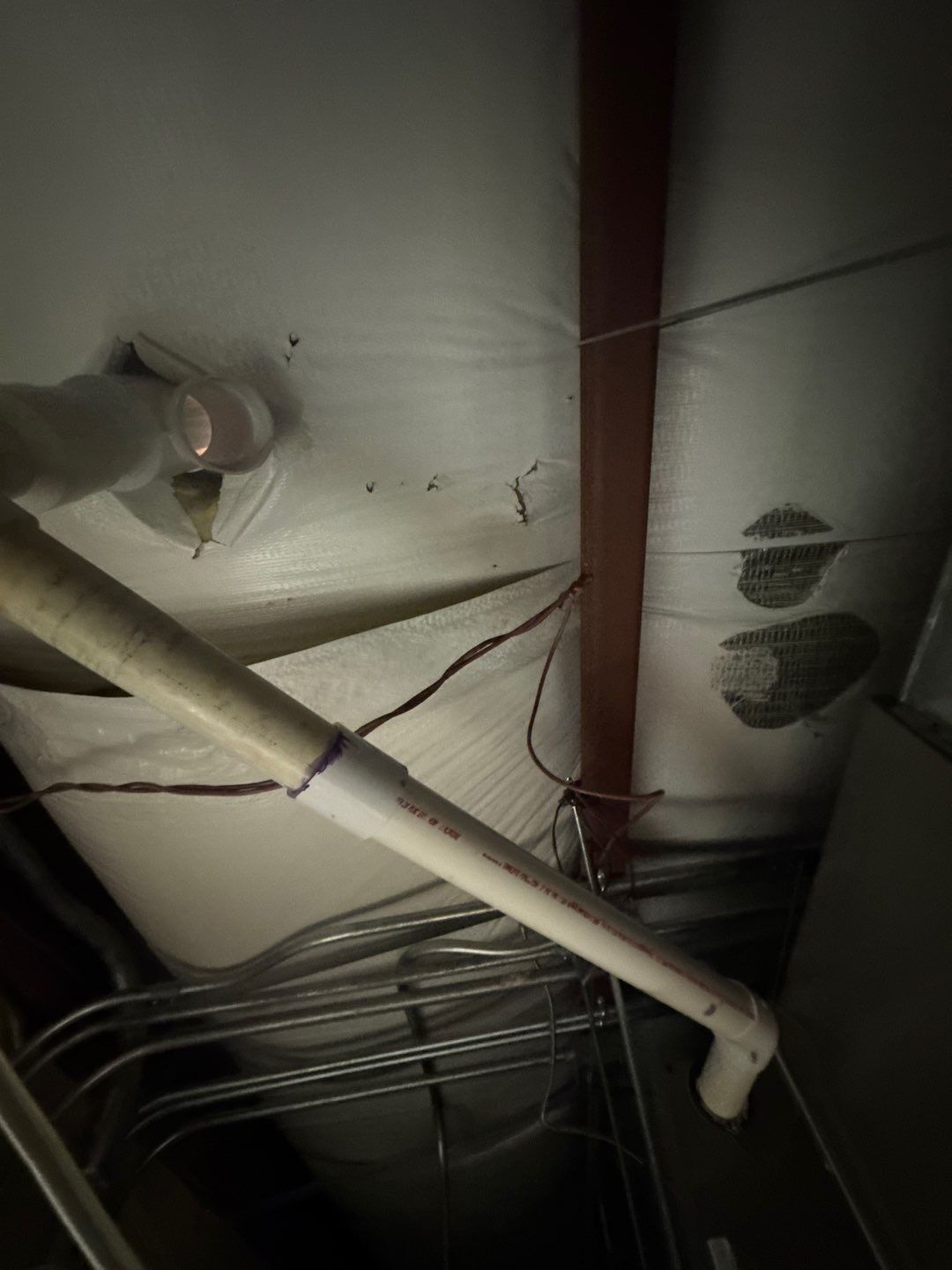
Figure 1: Sagging insulation shows either a leak or a condensation problem
What is Roof Condensation? The Science Behind It
If you’ve ever left a glass of ice cold lemonade outside on a hot, humid summer day, you’ve seen condensation. The outside of the glass quickly attracts water which is called condensation. Condensation has a few requirements before it appears: a cold surface, a warm environment, and humidity.
In the case of our lemonade, the glass is a cold surface, the air is a warm environment, and the humidity in the air provides the necessary moisture. For a building with a metal roof for example, condensation will form if the roof is cold, the air around it is warm or warming up (such as when the day before was below freezing and today is 65 degrees Fahrenheit), and humid air is also touching the metal roof to provide the water for condensation (such as a humid interior to the building).
While the weather is not controllable, the other two factors, humidity and a cold surface, can be adjusted and controlled to some extent.
Manufacturing processes, cooking, poor ventilation in restrooms, etc. can provide high indoor humidity. If the humidity of the building cannot be adjusted, ventilation can help move the air quickly enough to reduce condensation and to dry up condensation as it appears. If the humidity is at a minimum and ventilation has been put in place but condensation still forms, insulation is the final controllable factor. Poor insulation creates a cold surface on which condensation can appear. If a surface such as the roof is properly insulated, this removes the cold surface and reduces the occurrence of condensation.
Why Roof Condensation Matters: Risks and Consequences
Structural Damage
Condensation damages the structural integrity of the building by weakening metal and wood surfaces. When it appears on metal within the building, condensation causes corrosion of metal components. The water from condensation sits on the same metal parts consistently which creates the perfect environment for rust to attack the metal. On wood, condensation causes rotting of wooden framing and sheathing. By rotting wooden parts and corroding metal parts, condensation slowly eats away at the building’s structure and puts additional strain on other metal and wood components that haven’t been affected by condensation yet.
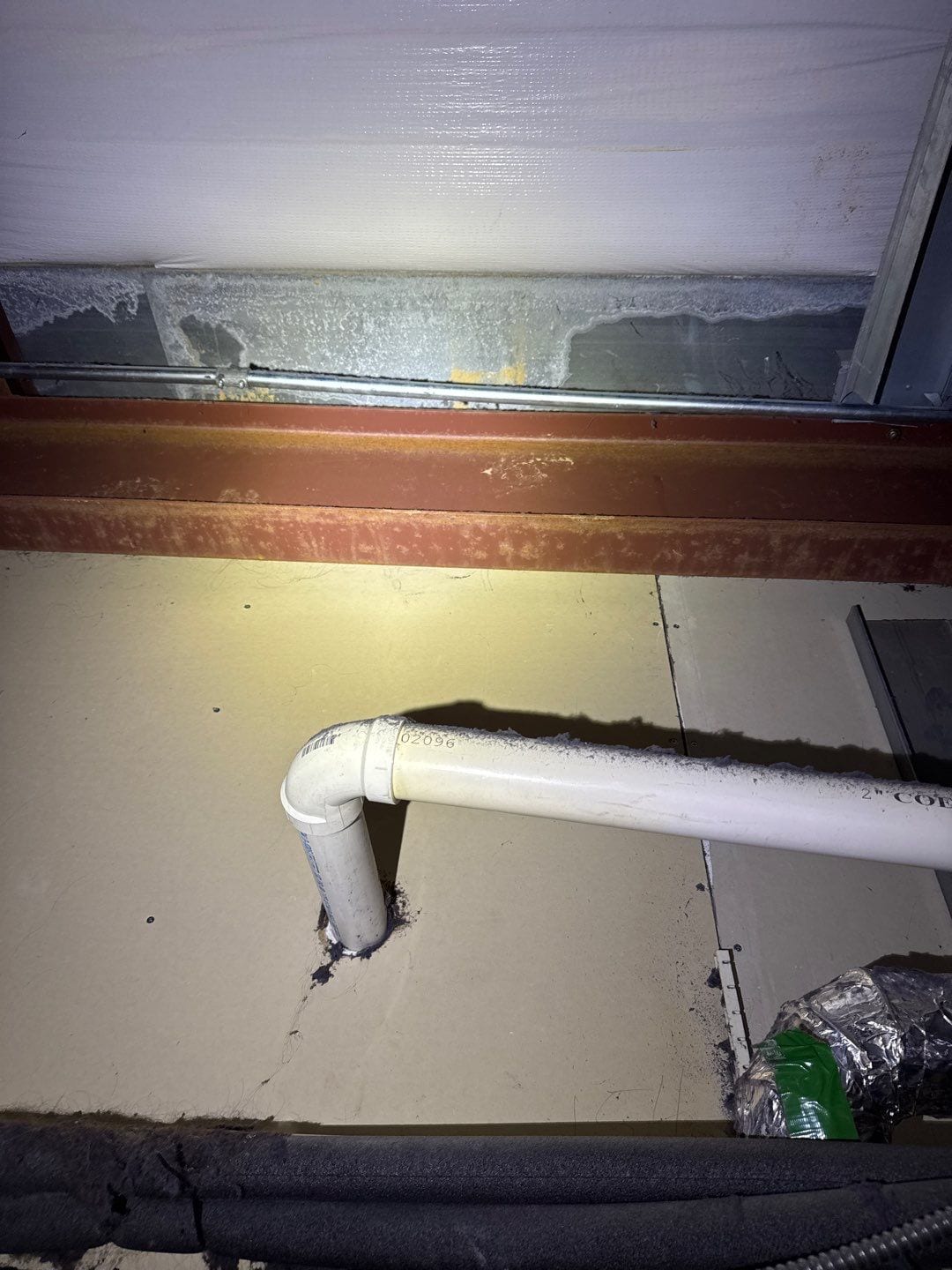
Figure 2: Condensation wearing away at the building’s metal structure by causing stains and rust
Mold and Mildew Growth
In addition to structural damage and strain, condensation creates an environment where mold and mildew grow. Mold and mildew are both health hazards for building occupants, create unpleasant odors, and stain surfaces, but remediation to thoroughly remove mold and mildew is costly.
Mold and mildew exacerbate pre-existing respiratory issues such as asthma and create respiratory issues in healthy individuals since they release mycotoxins which cause coughing and wheezing [1][2]. Mold and mildew also cause psychological issues such as anxiety, depression, confusion, difficulty concentrating, exhaustion, insomnia, and weaken the immune system which speeds up the effects of the afore mentioned symptoms [1].
Although mold and mildew can be cleaned out, the remediation process to purge a building of all mold and mildew is costly due to inspection fees, removal processes, safety, and material replacement to repair structural damage. Addressing moisture issues proactively is key to preventing these costly problems.
Reduced Insulation Effectiveness
In addition to health concerns and structural damage, condensation causes wet insulation. When insulation becomes wet, its effectiveness is hampered which costs building owners additional money through energy loss. When insulation is wet, it loses its R-value which is to say that its ability to block heat transfer (either keeping heat in during the winter or keeping heat outside of the building during the summer) is reduced. By decreasing R-value, energy bills increase. If the area where condensation appears is small, it may be an unnoticeable change in bills but, the larger the area affected by condensation, the higher the energy bills reach.
Decreased Property Value
Finally, over time, condensation reduces property value and property appeal to both customers and potential property buyers. Since condensation causes mold, customers will be less likely to enjoy the experience of visiting or shopping in the building. Potential buyers will see mold as a health issue that they may not want to deal with and the structural damage as an investment risk.
Hiring employees may also be difficult due to the health concerns around working in an environment with mold. Mold growth in a building can reduce a business’s ability to function profitably by making hiring more challenging and reducing customer engagement while also making it difficult to escape the building if buyers are not interested in purchasing the property.
Spray Foam and Spray-On Roofing Systems: A Solution to Condensation
Preventing Condensation in Commercial Roofs with Spray Foam
One way to prevent condensation is to install a spray foam roofing system on your roof which is what SR Commercial Roofing specializes in. Spray foam is sprayed as a liquid which quickly expands to form a rigid foam, called “Closed-cell foam.” Spray foam roofing systems seal a roof against leaks, but more importantly, it insulates the roof which reduces condensation. By insulating your roof, the roof will not fluctuate temperatures with the weather as quickly which significantly reduces the incidence of condensation.
Condensation forms when the roof is cold but the air surrounding it suddenly becomes warm so that water forms on the metal within the building. However, when a roof is insulated with spray foam, the metal roof’s temperature stays more similar to the internal temperature of the building which reduces condensation’s ability to form within the building. If condensation were to form on top of the spray foam which now covers the roof, it would quickly dissipate by running off the roof due to sloping that we ensure as we apply foam or the sun would dry it out. But a spray foam roofing system will not be damaged by condensation since it is waterproof when protected by industrial grade roof coatings.
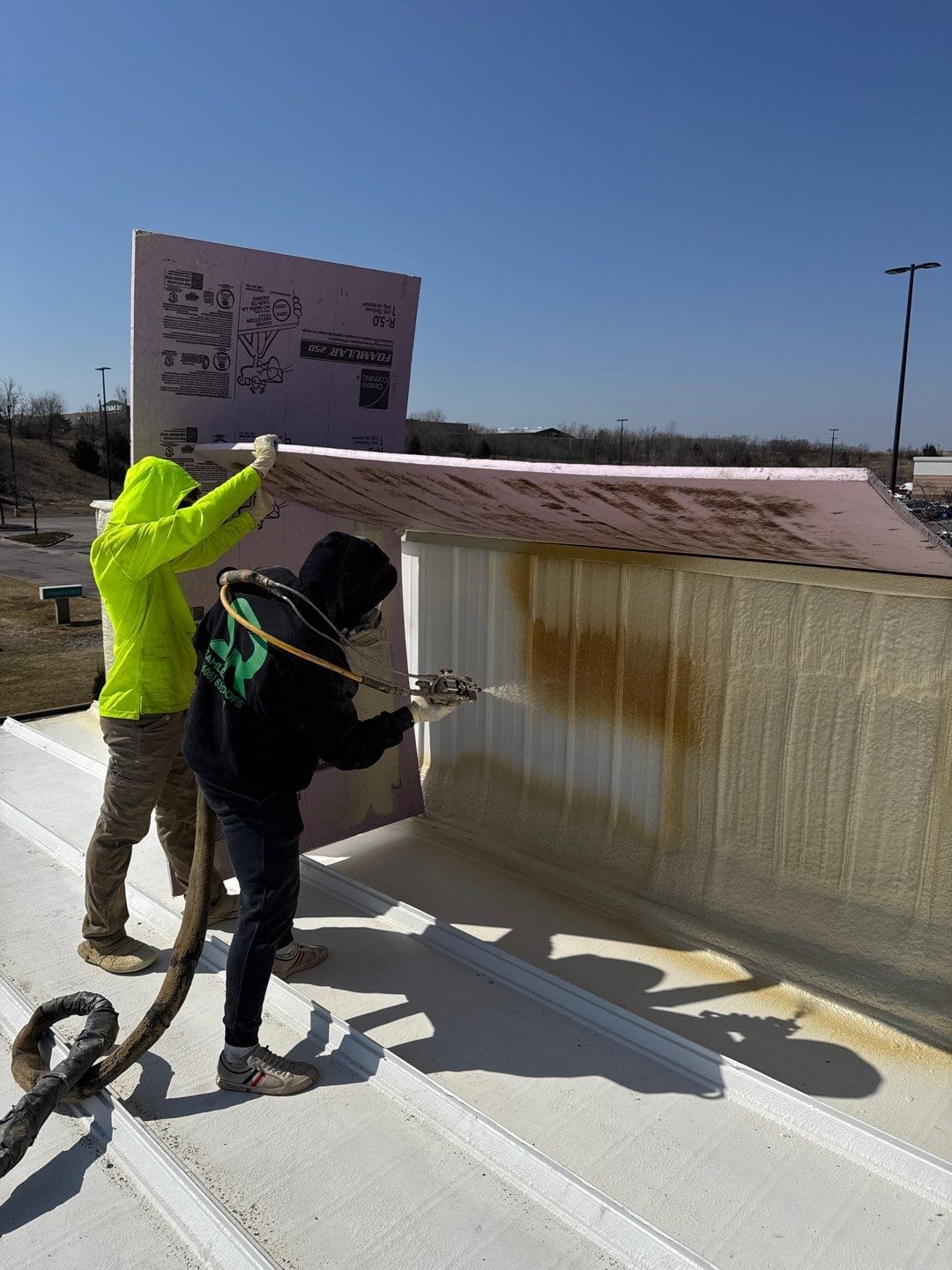
Figure 3: Foaming on the roof to prevent condensation
Benefits of Spray Foam Roofing Systems
Spray foam roofing systems reduce ponding water, prevent leaks, and improve insulation. Spray foam roofs protect against leaks by offering a seamless, waterproof barrier which blocks water and protects the roof’s structure. Also, when we at SR Commercial Roofing install spray foam roofing systems, we slope the finished product towards drains to reduce ponding water on flat roofs. Finally, spray foam roofs are great insulators with a high R-value of 9.6. The higher the R-value the better the insulator since R-value is a measure of a material’s ability to resist heat transfer. Spray foam insulation is key to preventing condensation in commercial roofs by reducing the metal’s temperature swings which reduces or removes the occurrence of condensation.
Conclusion
Condensation might seem like a minor issue compared to roof leaks, but its impact on your building can be just as significant—or even worse. Left unchecked, it can lead to structural damage, mold growth, and property value depreciation. The good news is that solutions like spray foam roofing and improved ventilation can effectively prevent condensation and protect your property.
At SR Commercial Roofing, we specialize in identifying and addressing condensation problems in commercial roofs. Whether you need help diagnosing the issue as a roof leak versus roof condensation or implementing a long-term solution, our team is here to help. Don’t wait until condensation compromises your building’s integrity—contact us at 608-844-4933 for a free inspection and to learn how spray foam roofing can make a difference!
—————————–
Citations
[1] https://nlr.com.au/articles/mould-exposure-long-term-side-effects
[2] https://axonintegrativehealth.com/blogs/the-long-term-health-effects-of-mold-exposure/