Roofs serve a simple yet critical role. All they need to do is keep the weather out of the building.
But, even with such a simple job, roofs need the strength to withstand weather, the flexibility to seal around roof protrusions, and the proper angles to direct water off the roof or into a drain which requires strong, yet flexible materials and good installation.
Even with careful installation and quality materials, leaks, ponding water, or holes in the roof can crop up. When unnoticed and not addressed, these issues can compromise the roof’s integrity, performance, and lifespan.
Some problems on roofs are the result of weather damage which is largely uncontrollable. However, other issues can be remedied with proper installation followed by regular maintenance, and even weather-related damage can be lessened with maintenance after the storm passes.
Let’s dive into some of the most frequent issues faced by commercial building owners and property managers:
Common Roof Problems
1. Leaks
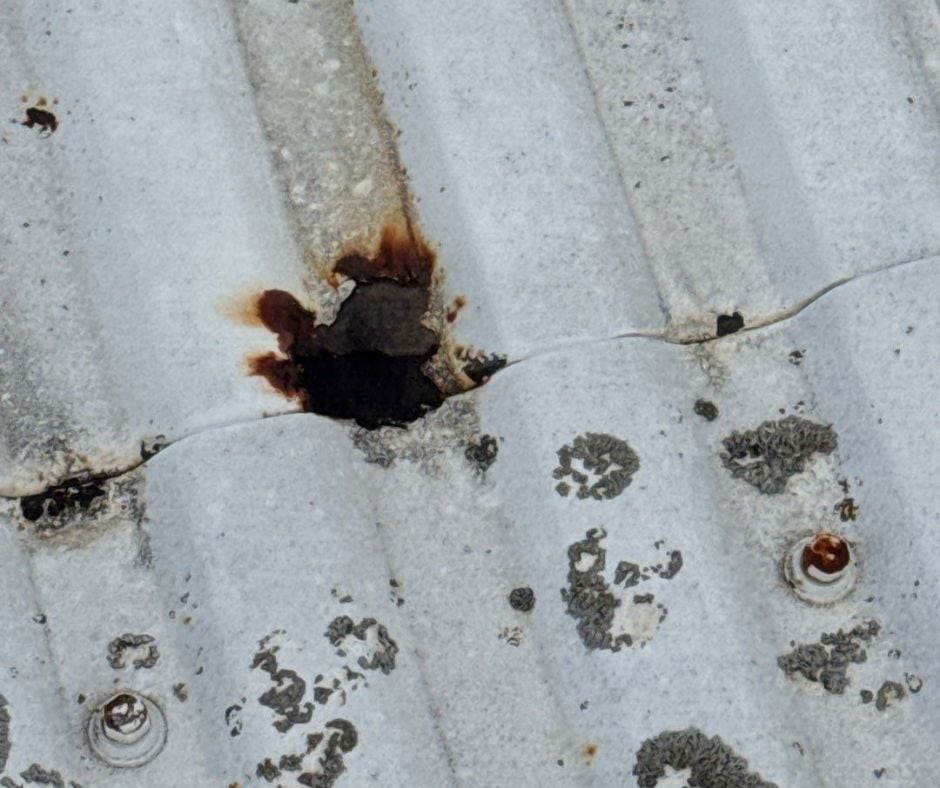
Leak caused by rusting metal.
Leaks are the most common roofing problem. They often appear after storms from wind, rain, or hail and after temperature swings. A leak may be created by a puncture in a rubber roof, a pinhole in a metal roof, cracks, unsealed protrusions, or near seams that are pulling apart.
When left alone, leaks cause water damage, mold growth, and structural deterioration. In the short term, leaks can be sealed using caulk to cover a puncture or pinhole or to seal a protrusion.
Besides weather and temperature changes, leaks are often the result of not addressing the issues mentioned below. When those problems are not solved, leaks are a common consequence.
2. Ponding Water
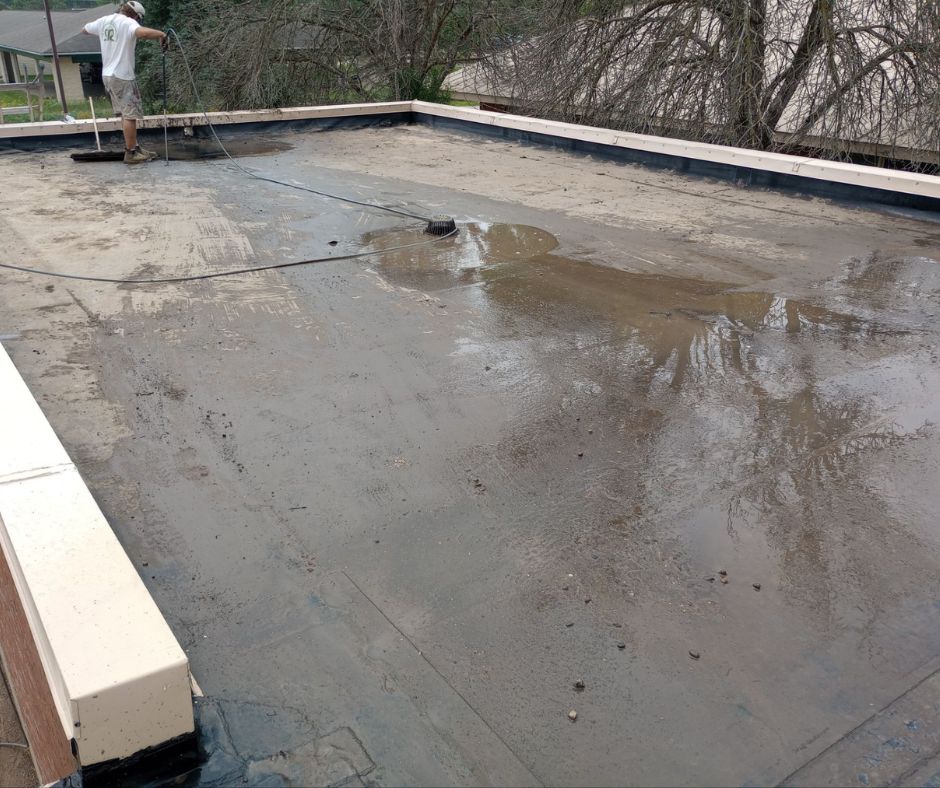
Water ponding on the roof.
Ponding occurs when water accumulates on a flat or low-slope roof due to inadequate drainage, clogged gutters, or a sagging roof.
The result of standing water is to accelerate membrane deterioration and rusting, promote algae and vegetation growth, increase roof weight which can lead to a cave-in, create leaks, and cause structural damage.
In the short term, dry ponding water and clean the roof to remove mold and mildew which will slow or prevent deterioration.
Long-term solutions include re-sloping: tear off the old materials and install a new one with proper drainage. Or hire a company, like SR Commercial Roofing, who sprays 1-1/2” of roof foam on the roof which can be shaped and angled to create proper drainage before coatings seal the foam and the roof from weather.
3. Thermal Bridging
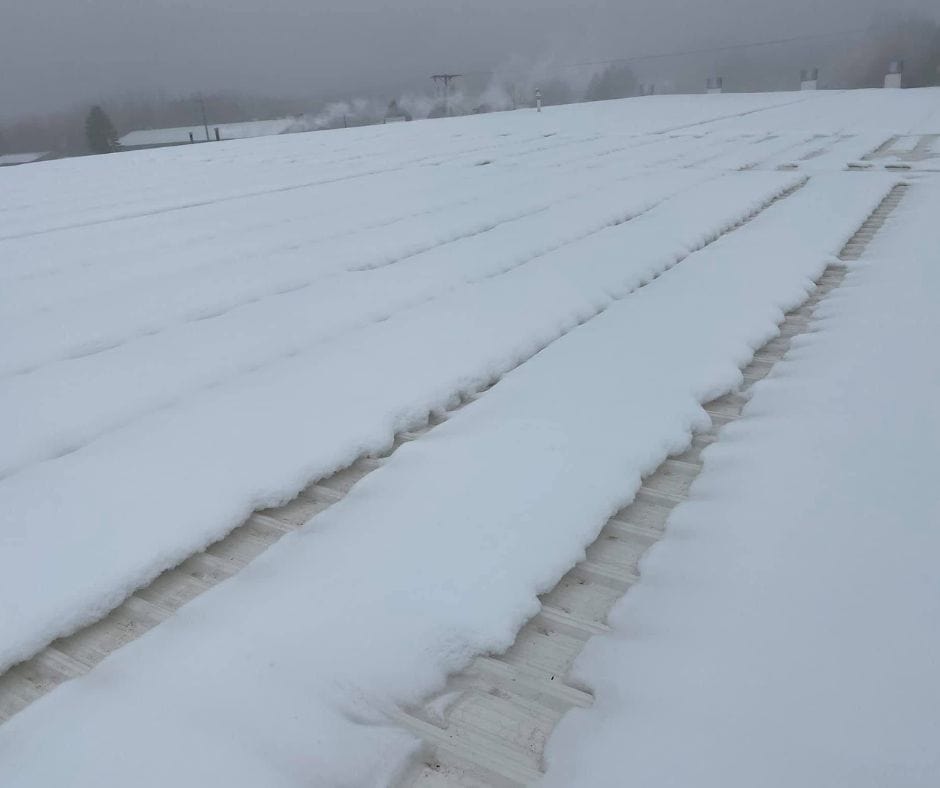
Snow unevenly melting on a roof due to heat escaping.
Thermal bridging is when heat exits or enters a building through conductive materials (often wood or metal) in the roof structure and bypasses insulation. The heat lost can be up to 30% which dramatically increases energy costs and creates temperature imbalances which often lead to condensation within the building [1].
To remedy heat loss, add additional insulation to the inside of the building, especially around wood and metal support beams that touch the roof, but the insulation may need to be checked regularly to ensure the insulation is not merely absorbing the condensation.
To remedy condensation, in addition to the extra insulation afore mentioned, increase ventilation to the area to quickly remove any condensation which will lessen structural damage caused by condensation.
Another option to reduce heat loss and stop condensation is to hire a company to install spray foam on top of the roof which evenly insulates the entire roof to prevent heat loss and condensation.
4. Deterioration and Defects
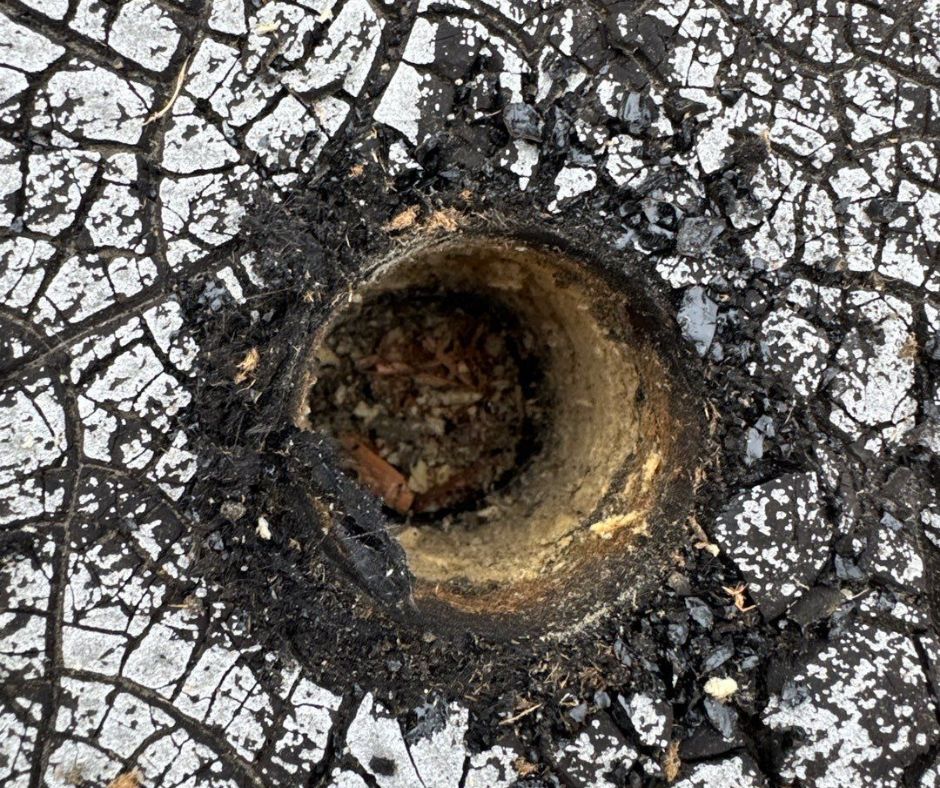
Deteriorating tar roof.
Rubber roofs, tar roofs, and coatings can suffer from blistering (bubbles caused by trapped moisture or air), alligatoring (cracking resembling alligator skin due to aging and UV exposure), shrinkage (contraction causing gaps and tears), splits, tears, and exposed laps. These deteriorations and defects weaken the roof’s ability to keep water out and make leaks more likely.
Rubber and coating deterioration can be caused by improper installation, product defects, or old age. For example, when roof coatings are sprayed over a dirty or wet roof, then they do not properly adhere to the roof and peel off with temperature fluctuations and weather.
In other cases, the quality of the material from the manufacturer is poor or defective, in which case, a warranty ought to cover the roof, and the coatings and/or rubber ought to be replaced by the roof installer.
Finally, rubber roofs and coatings decay and fail with age. Depending on the quality and warranty of the coating or rubber, this decay may begin to appear anywhere from 10-20 years after installation but is to be expected after the warranty expires.
5. Flashing & Penetration Issues
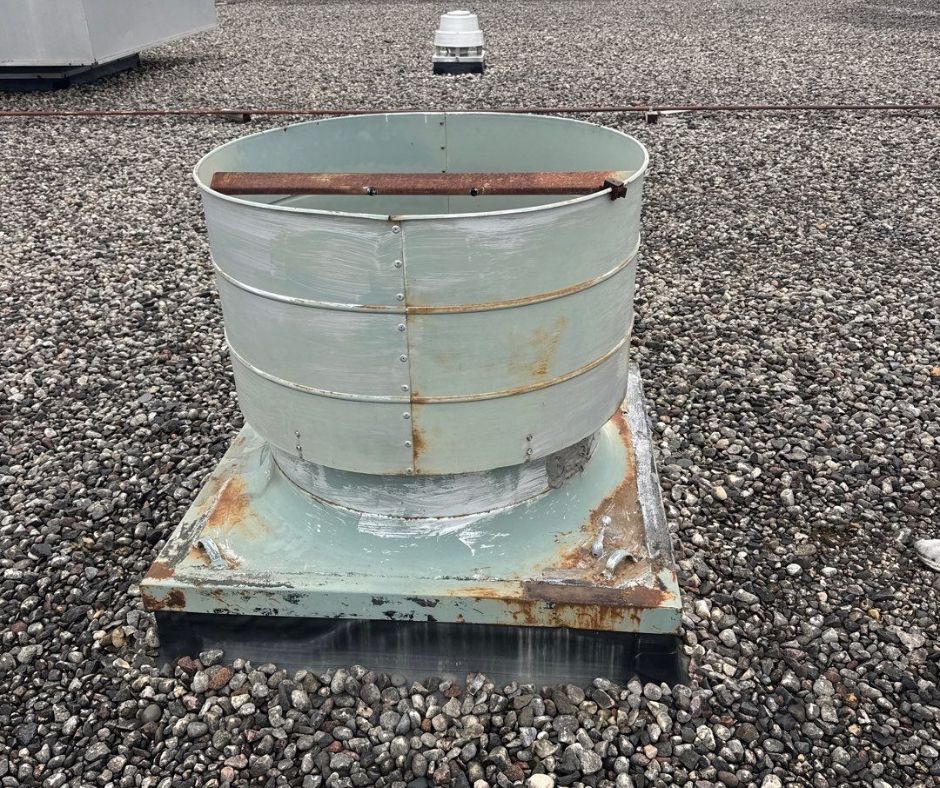
Roof protrusion.
Flashing is a strip of metal that seals joints and roof penetrations (such as vents, HVAC units, and skylights). Damaged, improperly installed, or deteriorated flashing is a common source of leaks because often the flashing will pull away from the penetrations and allow water to slip into the building.
One solution is regular maintenance: caulk around the protrusions to seal them to the flashing.
Another option is to use a fabric reinforcement around drains or protrusions and spray a coating over the fabric to make a waterproof barrier – which is the process we use to seal protrusions.
6. Weather-Related Damage
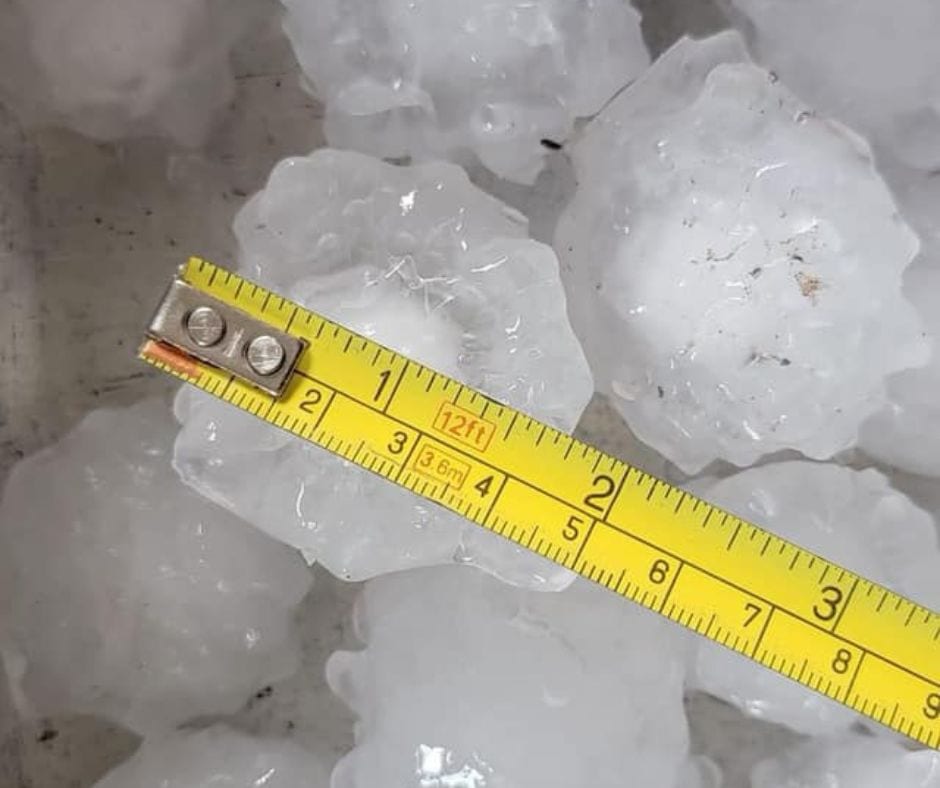
Large hail after a storm.
Exposure to harsh weather—UV radiation, heat, freezing temperatures, hail, wind, and storms—can cause roof cracking, blistering, rusting, and structural damage. Wind uplift can dislodge roofing materials like fasteners or pull seams apart, while hail and debris can puncture rubber roofs and put pinholes in metal roofs,
Regular maintenance to caulk or repair new leaks after a severe storm, to remove debris, and to clear away standing water will lessen the damage and extent of any leaks.
7. Clogged or Blocked Drains and Gutters

Clogged gutter.
Blocked drainage systems prevent proper water runoff leading to ponding and accelerated roof deterioration.
Regular cleaning and maintenance to clear the roof and gutters of debris are essential to prevent water accumulation and leaks.
How SR Commercial Roofing Addresses These Problems
For leaks, SR Commercial Roofing typically washes and dries the roof, caulks screws, applies fabric over seams and protrusions, and coats the entire roof to create a waterproof barrier.
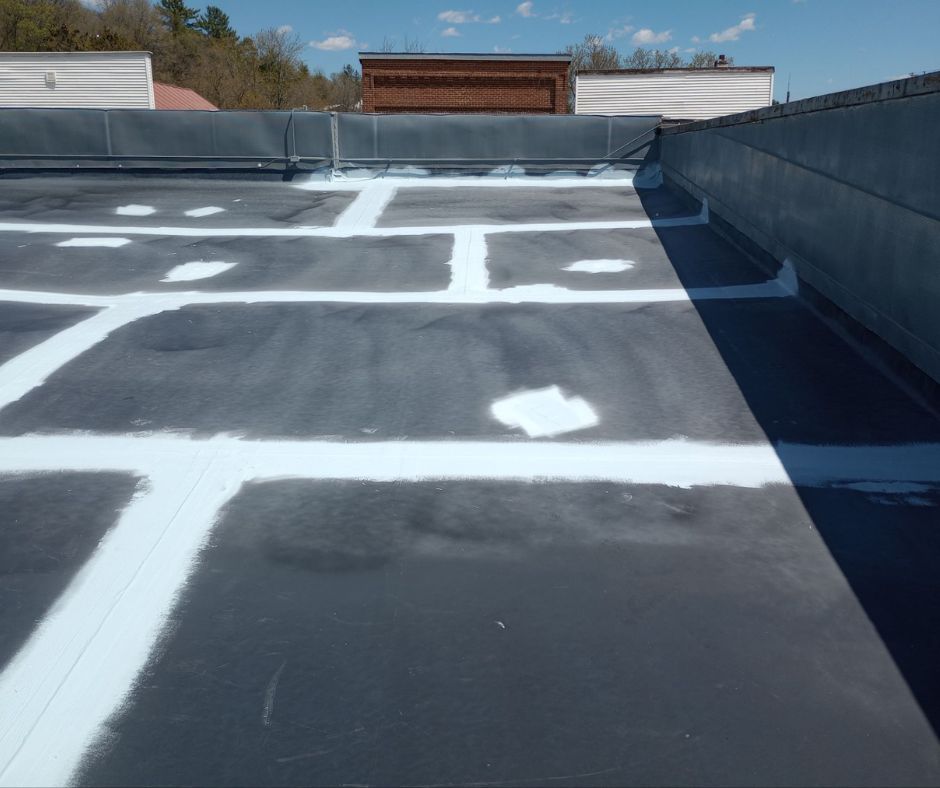
Fabric laid over seams with coatings sprayed over the fabric.
For structural damage, thermal bridging, and ponding water, spray foam is an additional phase in SR’s spray-on roof application. Spray foam adds additional strength to the roof to reduce strain caused by structural damage. It also insulates the roof which reduces heat loss and condensation. Lastly, it can be thoughtfully applied to create proper drainage for water into a drain or off the roof.
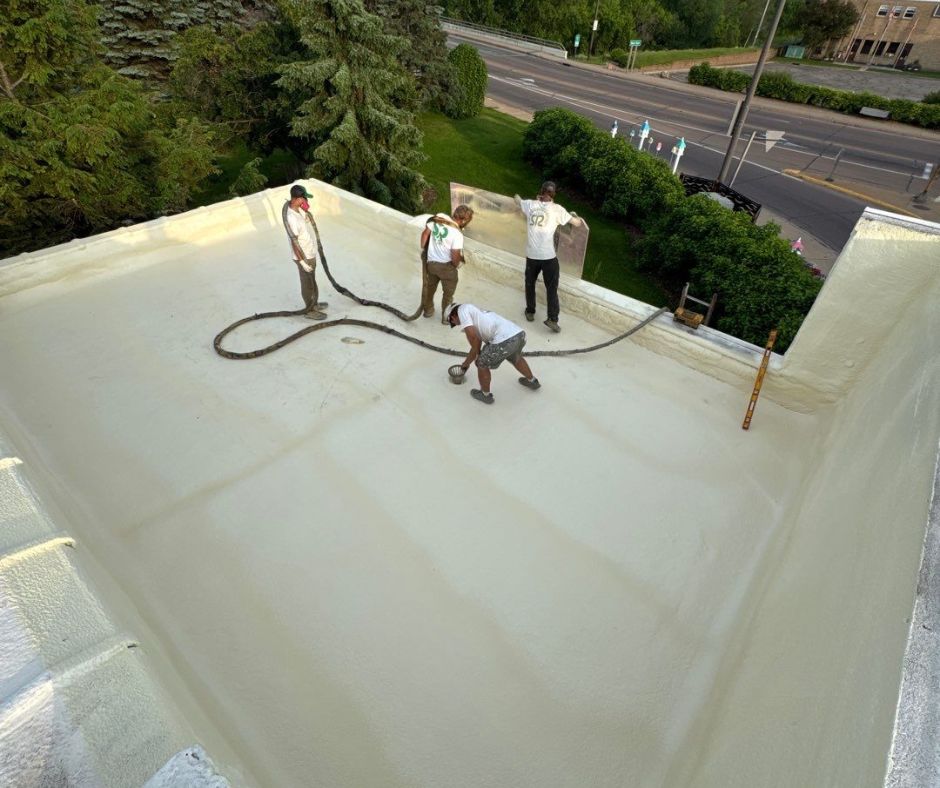
Spray foam installation in progress.
What Can I Do to Prevent These Problems?
Proper installation is critical for a long-lasting roof. Maintenance can extend a roof’s life but cannot fix problems caused by poor installation. When choosing a roofing company, look for consistency and quality. Large companies may have multiple crews with varying standards, but small businesses like SR Commercial Roofing have a single, experienced team that handles every job with care and excellence. Ask potential contractors about their approach to preventing leaks, preparing surfaces before coating, addressing ponding water, and managing heat loss and condensation.
Questions you can ask a contractor to probe their knowledge can include the following:
- How do you prevent leaks from occurring around protrusions, seams, endlaps, etc.?
- If applying a coating, what prep do you perform before spraying the coating onto the roof? (Do they wash and dry the roof and ensure enough time for the coatings to dry between applications?)
- How do you prevent ponding water?
- What are your recommendations for avoiding heat loss and condensation?
- What type of weather is harshest on the roof you install (whether it be a metal roof, rubber roof, spray foam roof, or a spray-on coatings roof)?
- How many crews do you have? Do they have any training?
Regular Roof Maintenance
To keep your roof in top shape, perform these maintenance tasks:
- Caulk pinholes, punctures, seams, and protrusions as soon as leaks occur.
- Dry ponding water and clean the roof to remove mold and mildew.
- Install proper insulation to prevent heat loss and condensation.
- Improve ventilation to remove condensation quickly.
- Schedule yearly maintenance checks with a professional to inspect, clean, and reseal your roof as needed.
Some companies offer yearly maintenance on a roof which may include checking the roof annually for leaks, cleaning the roof, and resealing any leaks or protrusions with caulk, fabric, and coatings.
Conclusion
A healthy roof is vital for protecting your property and ensuring comfort year-round. By understanding common roofing problems and investing in quality installation and maintenance, you can extend your roof’s lifespan and avoid costly repairs.
For commercial roofing solutions that combine expertise, reliability, and a commitment to excellence, we at SR Commercial Roofing would be delighted to work with you to solve your roof issues. Our dedicated team delivers lasting results and peace of mind for every project. Contact SR Commercial Roofing to keep your roof—and your business—covered.
————————————-
Citations: